Concept.
I referenced similar elements and aesthetics from other seats in our rigid kayak line. Keeping the design minimal, I limited the seat to only essential components, a frame, mesh, and recline straps to keep the seat lightweight. The seat also needed to be compact to fit inside the bag with the deflated kayak. The materials for the mesh were chosen to deliver the ultimate comfort, withstand corrosive environments and drive the aesthetics. Under my contract, I can’t show sketches for the form development of the seat.
Prototypes.
The primary prototype was made by 3D printing our tube sections that were adhered together to make a back and bottom frame. The frames were fiberglass together for testing. Secondary prototypes were made by cutting apart old seat samples that were re-welded.
Samples.
Five seat samples were made. All samples used anodized 6061 T6 aluminum frames, Ripstop Nylon + Monomesh inlaid seat skins. I handled the sourcing and coordination of samples with vendors. Seats are manufactured at the same factory as the bag. One year of testing showed insufficient structure in the mesh pattern. Updated patterns were designed and sampled for one year. Materials were tested in highly corrosive and UV scenarios. Accelerated weather testing was also used to qualify materials.
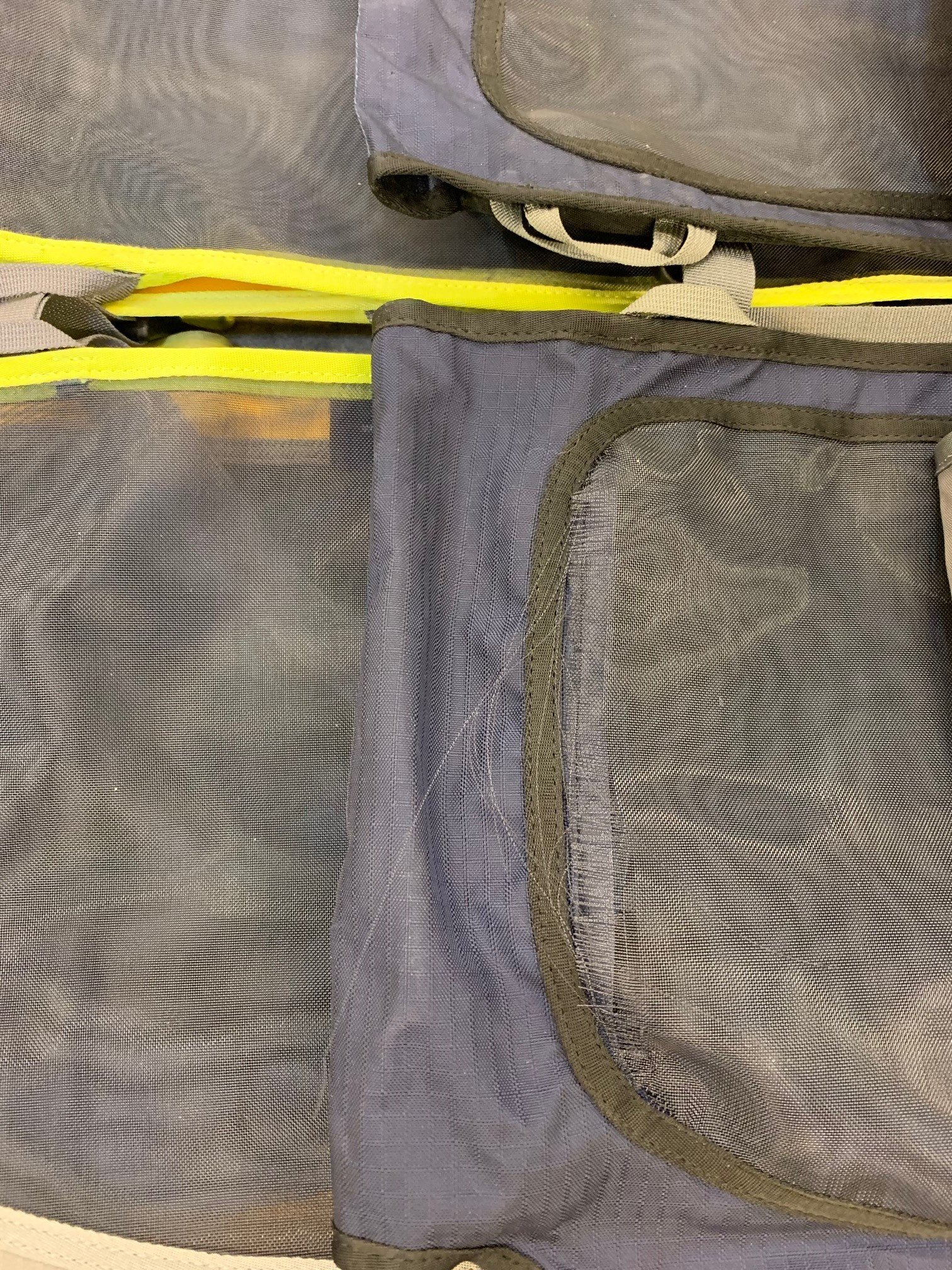
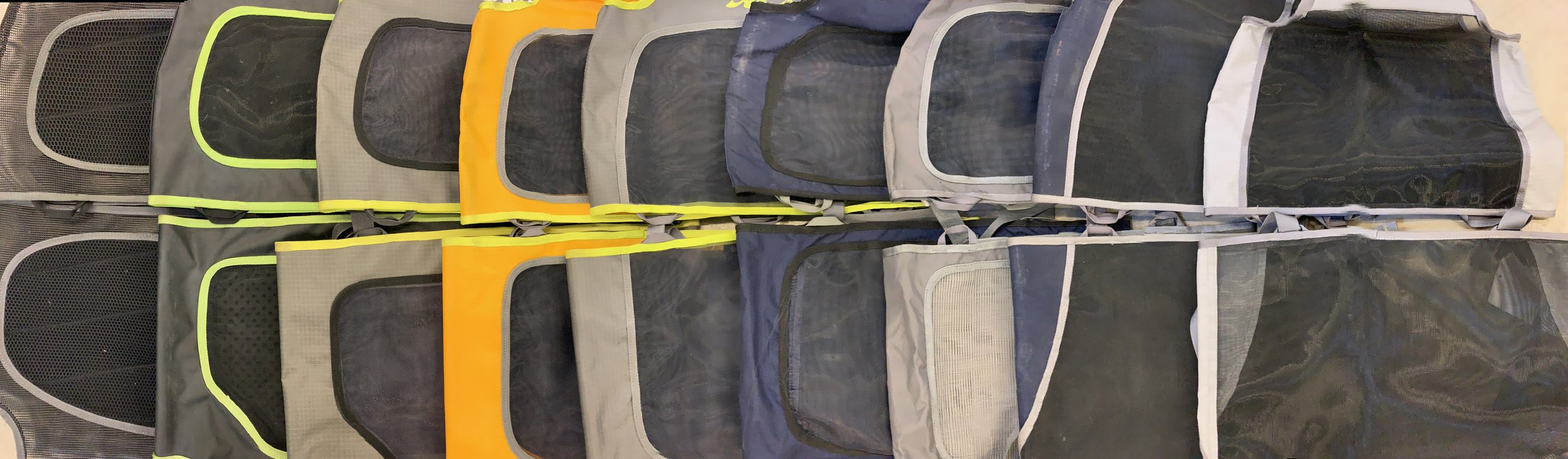
Load Testing.
With quality being a primary attribute, I set up a cycle test to drop 300lbs on the seat 10,000 times. The seat and mesh passed without any failure giving us the confidence to keep our progression toward production.
Production.
Vendor met delivery date for 1st and 2nd PO, 3rd and 4th PO was delayed by Covid-19 and limited workforce at factory. Production units met and continue to exceed the quality expected.
-
Hull
-
Steering
-
Bag
-
Interface
-
Industrial Design